Despite strong retail sales, the lumber market made a retreat in June as dealers withheld from buying anything unless absolutely necessary. The result was a growing stock pile of lumber at mills and reloads, and a growing sense of desperation from the same to move inventory before the market lost any more ground. In June of 2021, the market quickly deflated from historic heights after dealers, who over-estimated their needs and projected demand (but had to contend with escalating costs and outages), became swamped with inventory purchased as a result of panic-buying. This year, dealers were plagued with the backwash of late deliveries, which rather unintentionally bolstered inventories as few orders arrived when anticipated due to the extreme lack of transportation resources, making it commonplace for lumber and plywood orders (which, under normal circumstances, have two to three week lead times) to arrive four, five, six (and even more) weeks late. With the uncertainty of arrival times, dealers were forced to order stock from distributors who could cover their needs in a prompt manner. The result was that once late trucks did arrive, dealers ended up having larger stock inventories than desired, eliminating the need to replenish. In addition (and quite unlike last year), the weight of economic uncertainty is getting heavier, as escalating fuel prices, increasing borrowing costs, stock market retraction, recession concerns, and a growing malaise in home buying in general has curbed much of the confidence the industry has enjoyed of late. Nonetheless, retail sales remain strong and so dealers have recently jumped in to replenish and cover their needs in the face of waning surplus stock and upcoming mill shut downs. As of print, pricing has firmed but lead times and availability are still favorable. How long this lasts and what direction the market goes from here remains to be seen, but we anticipate that pricing will remain flat but firm throughout July as the balance between supply and demand equalizes.
As we all know too well, a big part of buying and selling building materials is dealing with problems. Plenty can go wrong and it often does. Nonetheless, when attention or action needs to be taken to address a situation, it’s critical to gather as much information as you can to convey what the issue is and what product is affected. When it comes to lumber, it starts with identifying the mill, which can often be easier said than done as, unlike some of the heavily branded products that come with obvious labels (such as Andersen or Thermatru), lumber items such as framing and plywood, out of their wrapper, can oftentimes be difficult at best and impossible at worst to identify. The key in these cases is to try and locate the grade stamp, which indicates not only the origin of the producing mill, but also important information required to ensure that every piece is appropriate for its end use. That little grade stamp is packed with a lot of important information, such as the mill identification name or number, the grading association (such as the National Lumber Grade Authority Rule (NLGA) or the Western Wood Products Association (WWPA)), the species of lumber (most commonly, S-P-F for spruce-pine-fir), the grade itself (such as No. 1 or No.2) and the treatment, such as KD (kiln dried), HT (heat treated) or GRN (green). Other stamps that may be present could be “Premium” (which isn’t an actual grade, but a product that is selected for a better appearance), S-Dry (“surface dry”, less than 19% moisture content), S-Grn (“surface green”, greater than 19% moisture content) and sometimes the mill’s logo. If you have any comments (pro or con) or concerns with the product, be sure to take a photo of the grade stamp along with photos of the issue (incorporating tape measures to illustrate dimension issues, sightlines to show proof of warp, twist or cup, or defects such as cracks, checks, splits or knots) and send them to us. We can then trace it back to the mill of origin. We promise you that we will take prompt action on the matter, and your photos will help us isolate the issue so that, if we have to perform an exchange of material, we can prevent you from getting inconvenienced a second time.
We buy from the suppliers that have the best reputations in the industry as we know the intrinsic value of selling quality products. Fewer call backs, better project results, and happier customers. Nonetheless, there is always a small percentage of production from every lumber supplier that pushes the limits of the grade. If it becomes excessive, that’s a problem and the key to a quick resolution is conveying as much information as possible upon the initial report, so that we can respond promptly based upon the facts provided. Thank you for your business!
Example of a Lumber Grade Stamp, Courtesy of the Maritime Lumber Bureau (MLB):
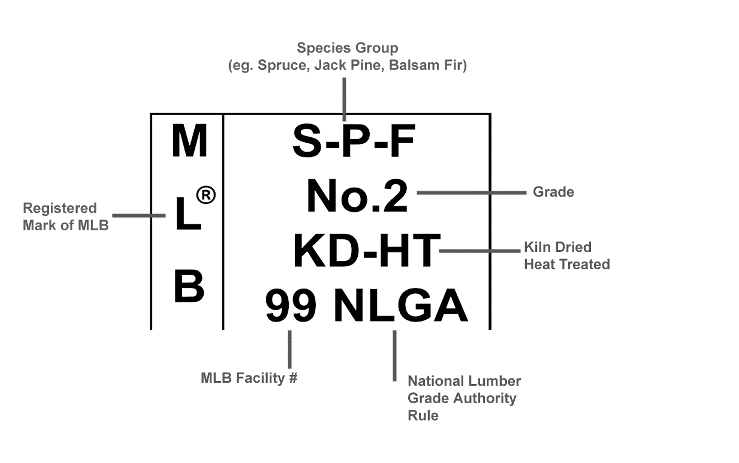